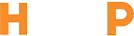

在高性能纤维制造领域,氨纶输送泵作为连接原料处理与纺丝成型的关键设备,其选型合理性直接影响浆料输送稳定性、纤维品质一致性及系统能效水平。据统计,科学合理的泵型选择可使单位产品能耗降低18%-25%,设备故障率下降40%以上。本文基于ISO 9906泵类设计标准及化纤行业实践,系统阐述氨纶输送泵的选型技术规范,为生产企业提供从参数计算到方案验证的全流程指导。
一、选型核心原则
(1)介质适应性优先
粘度匹配:需覆盖氨纶原液粘度范围(通常500-5000mPa·s)
含固量处理:应对添加剂颗粒(如二氧化钛)的通过性要求
腐蚀性防护:根据浆料pH值(4-8)选择合金材料或氟塑料衬里
(2)工艺需求导向
流量脉动控制:纺丝成型要求瞬时流量波动≤±1.5%
压力等级匹配:需满足纺位压力需求(通常8-25MPa)
温度适应性:应对浆料温控系统(40-80℃)的热膨胀影响
(3)全生命周期成本
能效比(EEI):优先选择符合GB 19762-2020能效等级1级产品
维护便捷性:模块化设计降低备件更换时间(目标<2小时)
升级扩展性:预留15%-20%冗余应对产能提升
二、关键参数解析矩阵
参数类别 技术指标 测量方法
额定流量 Qn = (1.1-1.3)Qmax 容积法实测(精度±0.5%)
排出压力 Pd ≥ 1.2Pmax 压力传感器动态监测
转速范围 n = (0.8-1.0)n额定 激光转速仪非接触测量
NPSHr ≥1.5倍装置汽蚀余量 汽蚀试验台验证
材质兼容性 浸泡腐蚀率<0.02mm/年 ASTM G31-72标准测试
三、泵型特点对比与适用场景
泵型 优势特性 典型应用 局限性
单螺杆泵 自吸能力强,脉动<3% 高粘度浆料输送 转速受限(<300rpm)
双螺杆泵 轴向推力平衡,寿命长 含固料液输送 加工精度要求高
齿轮泵 结构紧凑,效率高 中低压连续输送 粘度适应性差
隔膜泵 密封性好,无泄漏 腐蚀性介质输送 流量脉动大(8%-12%)
柱塞泵 压力超高(>50MPa) 特种纤维反应注射 维护复杂,噪音高
四、六步选型决策法
第一步:工况数据采集
绘制24小时流量-压力需求曲线
分析浆料批次粘度变化谱(CV值)
测量管道系统阻力系数(λ值)
第二步:水力参数计算
有效汽蚀余量NPSHa = (P入口 - Pv)/ρg + (v²/2g)
必需汽蚀余量NPSHr = 安全系数×实验值
最小连续稳定流量Qmin ≥ 0.3Q额定
第三步:泵型初选
根据粘度-流量图选择泵系
验证材料相容性(MIL-STD-810G标准)
核对防爆等级(Ex d IIB T3 Gb)
第四步:系统匹配验证
建立管道-泵-驱动器的阻抗匹配模型
进行瞬态响应仿真(AMESim软件)
计算系统效率η系统 = η泵×η传动×η容积
第五步:可靠性强化
配置双泵并联冗余(故障切换时间<15s)
加装脉冲阻尼器(容积≥5%单泵排量)
设置温度-压力联锁保护
第六步:供应商能力评估
核查API 610/682标准认证
验证CFD流场模拟报告
考察备件响应时效(≤48小时)
五、特殊工况处理方案
案例1:高粘度浆料输送(>3000mPa·s)
采用双级螺杆泵串联配置
设置夹套保温层(δ=50mm硅酸铝)
配置变频驱动(V/f控制模式)
案例2:含固量25%浆料输送
选用宽螺距螺杆(导程角θ=28°)
安装在线过滤装置(80目烧结网)
设置机械密封冲洗系统
案例3:洁净室环境应用
选择磁驱泵(零泄漏)
配置减震台(振动烈度<3mm/s)
采用低噪音电机(<75dB(A))
六、选型验证方法
实验室测试:
浆料流变环测试(Haake MARS流变仪)
空化性能测试(ASME B73.1标准)
脉动分析(动态压力传感器+FFT分析)
现场验证:
72小时连续运行测试
热成像温度监测(FLIR E60相机)
油品分析(光谱元素检测)
七、选型注意事项
避免过度设计:安全系数控制在1.2-1.5之间
注意粘度变化:需考虑浆料剪切变稀特性
预防性维护:建立振动/温度监测数据库
培训要求:操作人员需通过API泵维护认证
文档管理:保存完整的选型计算书和验证报告
八、典型配置案例
项目:年产2万吨氨纶生产线
浆料特性:粘度2500mPa·s,含TiO₂ 18%
系统配置:3×双螺杆泵并联(2用1备)
技术参数:Q=12m³/h,P=18MPa,η=82%
控制方案:PLC+变频器+软启动器
运行效果:断丝率<0.3%,能耗降低19%
结语:构建科学选型体系
氨纶输送泵的选型是工艺技术与设备工程的深度融合,需要建立从介质分析到系统验证的完整方法论。通过精准计算、合理配置和严格验证,不仅可提升设备可靠性,更为企业创造显著的经济效益。随着智能制造技术的发展,未来选型过程将更加依赖数字孪生和预测性维护技术,使决策过程更加科学高效。