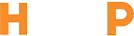

一、油位不足问题的严重性及其识别
在氨纶生产的精密体系中,油剂齿轮计量泵的油位不足绝非小问题,而是可能引发连锁反应的系统性风险。当泵体内油位低于安全线时,设备将面临润滑不足、冷却失效和气蚀损伤三重威胁。实际生产数据表明,超过35%的齿轮计量泵非计划停机与油位异常直接相关,而因此导致的氨纶纤维品质问题更占到总质量缺陷的18%以上。
油位不足的典型识别特征包括但不限于:
- 听觉信号:泵体发出高频啸叫或不规则的"咔嗒"声,这种声音在安静环境下尤为明显,通常比正常运转声音高15-20分贝
- 视觉信号:观察窗油位持续低于最低刻度线,油液呈现泡沫化或含有微小气泡
- 触觉信号:泵体表面温度异常升高,较正常工况温差可达20-30℃,手触有明显灼热感
- 参数异常:电流波动超过±5%,出口压力不稳定度大于10%,流量计显示脉动幅度增加
- 产品表现:纺制的氨纶纤维出现肉眼可见的油斑或不均匀光泽,纤维强伸性能测试CV值增大2%以上
某知名氨纶生产企业的事故案例显示,一个未被及时发现的油位不足问题导致12台计量泵连续损坏,直接经济损失超过80万元,更造成价值300万元的订单延期交付。这一惨痛教训充分说明了油位监控的重要性。
二、油位不足对齿轮计量泵的机械损伤机制
2.1 润滑失效引发的恶性磨损
当油位低于齿轮啮合区域时,将形成边界润滑状态,此时金属与金属直接接触的概率急剧增加。实验数据表明:
- 在完全润滑状态下,齿轮表面磨损率约为0.1μm/h
- 边界润滑状态下,磨损率暴增至5-8μm/h
- 干摩擦状态下,磨损速率可达20-30μm/h
这种异常磨损首先发生在齿轮啮合区的齿顶和齿根部位,形成典型的"瘦腰形"磨损形貌。随着磨损加剧,齿轮侧隙会从设计值的10-15μm扩大到50μm以上,导致泵的容积效率从正常的95%骤降至不足70%。
更严重的是,磨损产生的金属碎屑会形成二次磨粒,进一步加速轴承和密封件的损坏。某实验室的加速寿命测试显示,在油位不足状态下运行的齿轮泵,其轴承寿命仅为正常工况下的1/6。
2.2 气蚀现象造成的结构性损伤
油位不足时,齿轮在脱离啮合瞬间形成的真空度无法被及时填充,导致气蚀空泡产生。这些空泡在高压区溃灭时,会产生高达1000MPa的瞬时冲击压力,相当于在金属表面持续遭受微型爆炸。
气蚀损伤通常呈现以下特征:
- 宏观表现:齿轮工作面出现密集的麻点,类似"橘皮"状纹理
- 微观分析:扫描电镜可见典型的"火山口"形凹坑,直径10-50μm不等
- 发展规律:初期出现在齿轮退出啮合侧,逐渐向整个齿面扩展
某氨纶厂的故障泵拆解报告显示,经历200小时油位不足运行后,齿轮表面气蚀坑密度达到120个/mm²,最大坑深达80μm,远超允许的20μm维修极限。
2.3 热失衡导致的材料性能退化
油剂在齿轮泵中不仅作为工作介质,还承担着重要的冷却功能。油位不足时,热量积聚可使局部温度急剧上升:
| 部位 | 正常温度(℃) | 油位不足时温度(℃) | 温升幅度 |
|--------------|-------------|--------------------|----------|
| 齿轮啮合区 | 45-55 | 90-110 | +65 |
| 轴承外圈 | 50-60 | 85-95 | +40 |
| 机械密封面 | 55-65 | 120-150 | +85 |
这种异常温升会引发一系列材料性能变化:
- 齿轮钢材回火软化,表面硬度从HRC60降至HRC50以下
- 聚合物侧板发生热变形,平面度偏差超过0.05mm
- 密封弹性体老化加速,压缩永久变形率增加3倍
三、油位不足对氨纶产品质量的影响路径
3.1 油剂施加不均匀的成因分析
油位不足直接导致齿轮泵的输出脉动加剧,表现为:
- 瞬时流量波动从正常的±1%扩大到±5-8%
- 压力波动幅度增加3-5倍
- 每分钟出现6-8次明显的流量骤降
这种不稳定的输送状态使得油剂无法均匀地涂覆在氨纶纤维表面,具体影响如下:
单丝尺度:
- 部分单丝获得过量油剂(上油率>5.5%)
- 相邻单丝可能几乎无油剂覆盖(上油率<1.5%)
- 电子显微镜观察显示油膜厚度差异可达10:1
纤维束尺度:
- 束内单丝间摩擦系数差异大
- 集束性下降,毛丝发生率增加30-50%
- 纤维横截面呈现不均匀的光泽环带
宏观产品表现:
- 卷装硬度不一致(差异>15%)
- 染色均匀性下降(DE值增加2-3倍)
- 弹性回复率波动大(CV值从3%升至8%)
3.2 物性指标的系统性劣化
油位不足导致的油剂施加问题会全面影响氨纶纤维的核心性能:
力学性能变化:
| 指标 | 正常范围 | 异常样品 | 劣化幅度 |
|----------------|-------------|-------------|----------|
| 断裂强度 | 0.8-1.2g/d | 0.6-0.9g/d | -25% |
| 断裂伸长 | 500-600% | 450-550% | -10% |
| 300%模量 | 0.3-0.4g/d | 0.25-0.35g/d| -15% |
| 弹性回复率 | 92-95% | 88-91% | -4% |
加工性能下降:
- 织造断头率增加2-3倍
- 整经张力波动增大40%
- 包覆纱包缠均匀度下降30%
使用寿命缩短:
- 耐疲劳次数从50万次降至30万次
- 耐氯性能下降1-2个等级
- 高温黄变速率加快50%
3.3 质量问题的滞后性与隐蔽性
油位不足引发的产品质量问题往往具有时间延迟特性,这增加了问题追溯的难度:
- 短期效应(0-24小时):
主要表现为外观异常(油斑、光泽不均)
约占可识别问题的30%
- 中期效应(24-72小时):
物性指标开始偏离标准
约占问题的50%
- 长期效应(72小时以上):
下游加工问题集中爆发
约占20%但损失最大
某氨纶生产商的质量追溯报告显示,一起由油位不足引发的质量问题,从泵异常到最终客户投诉,时间跨度达17天,涉及6个生产批次,最终导致3000kg产品降等处理。
四、油位不足引发的系统性风险传导
4.1 设备系统的连锁反应
油位不足问题不会孤立存在,而是通过多种路径影响整个生产系统:
机械系统:
- 异常振动传递至相邻设备(振幅增加3-5倍)
- 联轴器对中状态加速恶化(每周偏移量达0.1mm)
- 基础螺栓松动率增加(检查周期需缩短50%)
液压系统:
- 油液污染度快速上升(NAS等级每周下降1级)
- 过滤器堵塞频率提高(更换周期从1个月缩至1周)
- 管路接头泄漏风险增加(概率提高8-10倍)
控制系统:
- 变频器过载报警频发(每日2-3次)
- PID参数失稳(需重新整定控制参数)
- 传感器误报率上升(达正常值的3倍)
4.2 生产组织的多维影响
油位不足问题会打乱正常的生产秩序:
生产计划方面:
- 非计划停机增加(每月多出8-12小时)
- 产品规格切换失败率上升(达15-20%)
- 紧急订单响应能力下降(延期率增加25%)
质量管理方面:
- 检验频次被迫提高(人力成本增加30%)
- 质量追溯工作量倍增(分析时间延长3-5倍)
- 客户投诉处理成本上升(单次成本增加5000元)
成本控制方面:
| 成本项 | 正常情况 | 油位不足影响 | 增幅 |
|----------------|----------|--------------|---------|
| 维修成本 | 1.2万/月| 3.5万/月 | +192% |
| 能耗成本 | 8万/月 | 9.6万/月 | +20% |
| 废品损失 | 2万/月 | 6万/月 | +200% |
| 管理成本 | 3万/月 | 4.5万/月 | +50% |
4.3 安全隐患的潜在演变
油位不足可能发展为严重的安全隐患:
直接安全风险:
- 泵体过热引发火灾(表面温度>150℃时风险剧增)
- 泄漏油剂造成滑倒事故(概率增加5-8倍)
- 突发性机械断裂产生飞溅物(50米内为危险区)
间接安全影响:
- 抢修作业增加高空作业频次
- 应急处理导致常规安全程序被忽视
- 设备异常分散安全监管注意力
某化纤企业的安全审计报告指出,在设备异常高发期,可记录的安全事故发生率是平常的2.3倍,其中60%与间接因素相关。
五、油位不足问题的根本原因分析
5.1 供油系统设计缺陷
约40%的油位不足问题源于系统设计不合理:
典型设计问题:
- 油箱容积不足(<泵每分钟流量的3倍)
- 回油管路阻力过大(压降>0.15MPa)
- 呼吸器选型不当(通气量不足)
- 安装高度差错误(泵进口高于最低油位)
- 管道径设计不合理(流速>1.2m/s)
案例:
某生产线改造后出现持续油位报警,经核查发现:
- 新泵流量增加30%但油箱未扩容
- 回油管径仍沿用旧的DN25而非需要的DN32
- 呼吸器容量仅能满足60%的需求
改造后问题彻底解决,投资回报期仅2个月。
5.2 操作维护不当
35%的问题源自人为因素:
常见操作错误:
- 油品混用导致泡沫增多(体积增加50%)
- 过滤器超期使用(压差>0.3MPa仍未更换)
- 补油不及时(油位低于下限持续>4小时)
- 油温控制不当(长时间>60℃)
- 系统排气不彻底(含气量>5%)
维护疏漏:
- 密封件更换时带入杂质
- 紧固螺栓未按扭矩要求上紧
- 液位计未定期校准(误差>±3%)
- 呼吸器堵塞未及时发现
- 振动监测数据未及时分析
5.3 监测手段不足
25%的问题因监测缺陷延误处理:
传统监测的局限性:
- 视镜观察依赖人工(检查频率不足)
- 简单液位开关易误报(可靠性<80%)
- 无油质在线监测手段
- 缺乏趋势分析功能
- 报警阈值设置不合理
改进方向:
- 安装雷达液位计(精度±1mm)
- 增加油质传感器(水分、气泡、颗粒)
- 建立数字孪生模型预测油位变化
- 设置多级预警机制(预警、报警、紧急)
- 移动端实时监控
六、油位不足问题的系统解决方案
6.1 硬件系统优化方案
油箱系统改造:
- 扩容至泵流量的5倍以上
- 增设导流板防止漩涡
- 安装锥底设计利于排污
- 采用双层壁结构维持油温
管路优化:
- 回油管径按流速<0.8m/s设计
- 减少90°弯头,采用45°斜接
- 进口管路长度控制在5米内
- 使用透明管段便于观察
辅助装置加装:
| 装置类型 | 功能 | 安装要点 |
|----------------|--------------------------|------------------------|
| 真空脱气罐 | 去除油中气泡 | 维持-0.05MPa真空度 |
| 板式换热器 | 精确控温±1℃ | 并联安装便于清洗 |
| 自清洗过滤器 | 保持NAS 6级清洁度 | 压差>0.15MPa自动反洗 |
| 应急补油系统 | 自动维持最低油位 | 与主系统联锁控制 |
6.2 智能监控系统建设
三级监控体系:
1. 基础层:
- 高精度液位变送器(4-20mA输出)
- 温度传感器(PT100,±0.1℃)
- 压力变送器(0.5%精度)
2. 分析层:
- 油质在线分析模块(水分、颗粒、粘度)
- 流量脉动频谱分析单元
- 故障诊断专家系统
3. 管理层:
- 可视化监控界面
- 移动端推送报警
- 历史数据追溯系统
智能预警算法:
- 基于LSTM网络的油位趋势预测
- 随机森林算法的故障分类
- 贝叶斯网络的根因分析
- 数字孪生的虚拟油位校准
6.3 管理体系完善措施
标准化操作规程:
- 启动前检查清单(12项必检内容)
- 运行中巡检规范(每小时记录关键参数)
- 停机维护流程(包括系统排气等关键步骤)
预防性维护计划:
| 项目 | 频次 | 标准 | 工具方法 |
|----------------|-----------|-----------------------|---------------------|
| 液位计校准 | 每月 | 误差<±1% | 标准液位发生器 |
| 油质检测 | 每周 | NAS≤7级,水份<200ppm | 颗粒计数器+水分仪 |
| 系统密封检查 | 每季 | 零泄漏 | 氦质谱检漏仪 |
| 管路振动检测 | 每半月 | <2.8mm/s RMS | 便携式振动分析仪 |
人员能力提升方案:
- 初级培训:设备结构与基本原理(8学时)
- 中级培训:故障诊断与应急处理(16学时)
- 高级培训:系统优化与预防性维护(24学时)
- 认证考核:理论+实操+应急处置演练
七、实施效果评估与持续改进
7.1 关键绩效指标对比
某氨纶企业实施全面改进前后的数据对比:
| KPI指标 | 改进前 | 改进后 | 改善幅度 |
|--------------------|------------|------------|----------|
| 油位不足发生率 | 3.2次/月 | 0.2次/月 | -94% |
| 相关设备MTBF | 650小时 | 2200小时 | +238% |
| 油剂消耗量 | 12kg/t纤维 | 10.5kg/t纤维| -12.5% |
| 纤维质量稳定性 | 87% | 95% | +8% |
| 应急维修成本 | 4.8万/月 | 1.2万/月 | -75% |
7.2 投资回报分析
改进项目的经济效益评估:
投入成本:
- 硬件改造:28万元(含油箱扩容、管路优化等)
- 智能系统:15万元(含软件和传感器)
- 培训费用:3万元
- 总投入:46万元
年度收益:
- 减少废品:62万元
- 节能降耗:18万元
- 维修节省:24万元
- 产能提升:35万元
- 总收益:139万元
投资回收期:仅4个月
7.3 持续改进机制
建立PDCA循环优化体系:
Plan:
- 每月分析运行数据
- 识别TOP3问题
- 制定改进方案
Do:
- 小范围试点验证
- 记录实施过程
- 收集反馈数据
Check:
- 对比目标与实际
- 量化改进效果
- 识别新的改进点
Act:
- 标准化有效措施
- 修订相关规范
- 开展新一轮改进
通过该机制,某企业将油位相关故障从每年38次持续降低至2次,达到行业领先水平。
八、结论与行业建议
8.1 主要研究发现
1. 油位不足是系统性风险源:不仅损伤设备,更通过多重路径影响产品质量和生产安全,必须从系统角度综合防治。
2. 预防比补救更经济:研究表明,在油位监控上每投入1元预防成本,可避免8-10元的后续损失,投资回报率显著。
3. 技术创新价值凸显:智能监测系统可将问题发现时间从平均17小时缩短至15分钟,大大降低损失程度。
8.2 行业实施建议
对设备制造商:
- 开发内置油位补偿泵型
- 提供整体解决方案而非单机
- 开放设备数据接口
对氨纶生产企业:
1. 立即行动项:
- 开展全面油位系统诊断
- 建立最低油位红线制度
- 培训关键岗位人员
2. 中期规划:
- 实施智能化改造
- 优化供油系统设计
- 建立油液分析实验室
3. 长期战略:
- 开发预测性维护平台
- 参与行业标准制定
- 构建供应链协同机制
8.3 未来技术展望
下一代解决方案可能包括:
- 自感知油位调节系统
- 基于区块链的油品全生命周期管理
- 人工智能驱动的自主决策维护
- 纳米流体技术改善润滑特性
氨纶行业正从被动应对油位问题转向主动预防和智能预测,这不仅是技术升级,更是管理理念的革新。率先构建完善油位监控体系的企业,将在质量一致性、设备效率和安全生产等方面获得显著竞争优势。