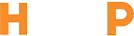

一、概述
丙纶输送齿轮泵是一种专门用于输送聚丙烯熔体的精密容积式泵,在化纤纺丝、非织造布生产等领域发挥着关键作用。作为丙纶生产线上不可或缺的核心设备,齿轮泵通过其独特的结构设计和工作原理,能够稳定、精确地输送高粘度、高温的聚丙烯熔体,确保后续纺丝或成网工艺的质量稳定性。
与普通齿轮泵相比,丙纶输送齿轮泵在材料选择、结构设计和制造工艺等方面都有特殊要求。由于聚丙烯熔体通常处于200-300℃的高温状态,且可能含有各种功能性添加剂,这就要求齿轮泵必须具备优异的耐高温性能、耐腐蚀性能和耐磨性能。同时,为了满足纺丝工艺对熔体输送稳定性的苛刻要求,丙纶齿轮泵的制造精度通常比普通工业齿轮泵高出一个数量级。
随着丙纶生产工艺的不断进步和产品品质要求的不断提高,对丙纶输送齿轮泵的性能要求也越来越高。现代丙纶齿轮泵正朝着高精度、高效率、长寿命和智能化方向发展,以满足日益严苛的工业生产需求。
二、丙纶输送齿轮泵的结构组成
1. 主要结构部件
泵体:作为齿轮泵的主要支撑结构,通常采用高强度合金钢或不锈钢整体铸造而成,具有良好的刚性和耐压能力。泵体内部分为吸入腔和排出腔,内表面经过精密加工以确保与齿轮的配合精度。为适应高温工作环境,泵体通常设计有保温夹套或加热装置。
齿轮副:这是齿轮泵的核心工作部件,由一对精密啮合的齿轮组成。主动齿轮通过联轴器与驱动电机连接,从动齿轮与之啮合旋转。齿轮通常采用优质合金工具钢或氮化钢制造,经过精密加工和热处理,齿形精度可达DIN 3级或更高。齿轮的轴向和径向间隙都经过严格控制,通常在0.05-0.15mm范围内。
轴承系统:负责支撑齿轮轴并承受径向和轴向载荷。由于工作环境温度高且可能接触熔体,丙纶齿轮泵的轴承系统通常采用特殊设计,如带冷却腔的双列滚子轴承或静压轴承,并配备高性能润滑系统。轴承材料多选用高温合金钢或陶瓷材料。
端盖:安装在泵体两端,与泵体共同形成封闭的工作腔室。端盖内表面通常设计有压力平衡槽,以减少齿轮的轴向推力。端盖与泵体之间采用高温密封垫片防止泄漏。
密封装置:防止高温熔体泄漏的关键部件。根据工作温度和压力不同,可能采用机械密封、填料密封或特殊密封形式。高温高压工况下,常采用双端面机械密封并配备阻封液系统,确保完全无泄漏。
2. 辅助系统
加热系统:维持熔体温度稳定的关键。泵体通常设计有夹套,可通入导热油或蒸汽加热。温度传感器和控制系统确保熔体温度保持在设定范围内,波动不超过±1℃。
润滑系统:对于大型高压齿轮泵,独立的强制润滑系统必不可少。它包括油泵、过滤器、冷却器和压力调节装置等,确保轴承和齿轮轴在高温下获得充分润滑。
清洗系统:用于停机后的泵体清洗,防止残留熔体固化堵塞流道。通常包括溶剂储罐、循环泵和喷嘴等,可进行CIP(在位清洗)操作。
监测控制系统:现代丙纶齿轮泵配备多种传感器,实时监测压力、温度、流量、振动等参数,并通过PLC或DCS系统实现自动控制和故障诊断。
三、丙纶输送齿轮泵的工作原理
1. 基本工作原理
丙纶输送齿轮泵属于正位移泵,其工作原理基于齿轮啮合过程中密闭容积的变化来实现熔体的吸入和排出。具体工作过程可分为四个阶段:
吸入阶段:当齿轮旋转时,在吸入侧齿轮逐渐脱离啮合,齿间容积增大形成局部真空,在压差作用下,聚丙烯熔体从进口管道被吸入齿间空间。
封闭输送阶段:随着齿轮继续旋转,吸入的熔体被封闭在齿轮齿与泵体形成的密闭空间内,并随着齿轮旋转向排出侧移动。此阶段熔体只随齿轮移动,容积基本不变。
排出阶段:当齿轮转到排出侧开始进入啮合时,齿间容积逐渐减小,对熔体产生挤压作用,当压力超过出口管道阻力时,熔体被强制输送到出口管路中。
过渡阶段:在完成一次排出后,齿轮继续旋转回到起始位置,准备下一个工作循环。设计精良的齿轮泵会确保各阶段平稳过渡,避免压力波动和流量脉动。
2. 流量特性
齿轮泵的理论流量Qt可由下式计算:
Qt = 2πm²zbn ×10⁻⁶ (m³/min)
其中:
m - 齿轮模数(mm)
z - 齿数
b - 齿宽(mm)
n - 转速(r/min)
实际流量Qa因存在内部泄漏(滑移量)而略小于理论流量:
Qa = Qt - C(ΔP/μ)
其中:
C - 泄漏系数
ΔP - 进出口压差(Pa)
μ - 熔体粘度(Pa·s)
丙纶齿轮泵的容积效率ηv通常在85%-95%之间,随粘度增加而提高,随压力升高而降低。
3. 特殊设计原理
高压设计:为适应纺丝工艺的高压需求(通常10-30MPa),丙纶齿轮泵采用多级减压设计:
- 齿轮采用小模数多齿数设计,增加密封线数量
- 严格控制齿轮与泵体的径向间隙(0.05-0.10mm)
- 采用轴向压力平衡结构,减小端面泄漏
低剪切设计:为避免聚丙烯分子链断裂:
- 采用大圆弧齿形,减小啮合冲击
- 优化齿侧间隙,减少熔体剪切
- 控制转速在适宜范围(通常50-200r/min)
温度控制:确保熔体温度稳定:
- 泵体加热夹套精确控温
- 轴承冷却系统防止过热
- 热隔离设计减少热传导损失
四、丙纶输送齿轮泵的特点
1. 技术特点
高精度:齿轮加工精度达DIN 3级以上,表面粗糙度Ra≤0.4μm,确保流量稳定性(波动<±1%)。
耐高温:采用高温合金材料,长期工作温度可达300℃,短时耐受350℃。
耐磨损:齿轮表面硬度HRC60以上,使用寿命可达10,000小时以上。
低脉冲:特殊齿形设计和多齿数结构使流量脉动<±2%,满足精密纺丝要求。
2. 性能特点
稳定可靠:平均无故障运行时间(MTBF)超过20,000小时。
调节方便:通过变频调速可实现流量精确控制(调节比10:1)。
维护简便:模块化设计使主要部件可快速更换,减少停机时间。
节能高效:容积效率>90%,比传统螺杆泵节能15-20%。
3. 应用特点
适应性强:可输送含30%填料的改性聚丙烯熔体。
工艺兼容:适用于熔融纺丝、熔喷非织造布等多种生产工艺。
规格齐全:流量范围从0.1L/min到5000L/min,压力最高可达50MPa。
五、选型与使用注意事项
1. 选型要点
流量选择:根据生产线产能确定,通常按最大需求量的120%选型。
压力等级:考虑系统总阻力,选择额定压力为最大工作压力的1.2-1.5倍。
温度范围:根据工艺温度选择合适的热处理等级和密封形式。
材料选择:根据熔体成分选择耐腐蚀材料,常规选用氮化钢,腐蚀性环境选用不锈钢或哈氏合金。
2. 使用注意事项
启动前:
- 检查旋转方向是否正确
- 预热泵体至工作温度(升温速率<50℃/h)
- 手动盘车确认无卡阻
运行中:
- 监控轴承温度(<75℃)
- 观察机械密封泄漏情况
- 定期记录运行参数
停机时:
- 先降转速再停机
- 保持加热至熔体排净
- 进行清洗操作防止残留
3. 维护保养
日常维护:
- 检查润滑系统油位和油质
- 紧固各部连接螺栓
- 清洁泵体外表面
定期维护:
- 每2000小时更换润滑油
- 每5000小时检查齿轮磨损
- 每年校验压力传感器和温度仪表
大修内容:
- 更换磨损齿轮和轴承
- 检查泵体磨损情况
- 更换所有密封件
- 重新校准对中
六、发展趋势
1. 智能化发展
在线监测:集成压力、温度、振动、泄漏等多参数传感器,实时监控泵状态。
预测维护:基于大数据分析预测部件寿命,提前安排维护计划。
自适应控制:根据熔体特性变化自动调整运行参数,保持最佳工况。
2. 新材料应用
陶瓷涂层:齿轮表面喷涂氧化锆或碳化硅涂层,提高耐磨性。
金属基复合材料:采用碳纤维增强金属基复合材料齿轮,减轻重量提高强度。
自润滑材料:开发含固体润滑剂的特种合金,减少润滑系统依赖。
3. 结构优化
微型化:发展小型精密齿轮泵,满足实验室和小批量生产需求。
集成化:将泵、电机、控制系统集成一体,减少安装空间。
模块化:标准化接口设计,便于快速更换和功能扩展。
七、结论
丙纶输送齿轮泵凭借其精密的结构设计和可靠的工作原理,成为聚丙烯纤维生产过程中不可或缺的关键设备。随着材料科学、制造工艺和智能控制技术的进步,现代丙纶齿轮泵在精度、效率和可靠性方面都达到了新的高度。正确选择和使用齿轮泵,不仅能够确保丙纶产品的质量稳定,还能提高生产效率,降低能耗和维护成本。未来,智能化、高效化和专用化将成为丙纶输送齿轮泵的主要发展方向,为化纤行业的技术进步提供更强有力的装备支持。