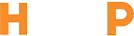

一、引言
在全球纺织行业竞争加剧和能源成本持续上涨的背景下,节能降耗已成为丙纶(聚丙烯纤维)纺丝企业的核心关注点。作为纺丝生产线的关键设备,齿轮计量泵的能耗直接影响整体生产成本。据统计,传统计量泵的能耗可占纺丝生产线总能耗的15%-25%,而高效节能型计量泵可降低能耗20%-40%,同时提升纤维品质。
本文将从结构优化、材料创新、智能控制、系统匹配等维度,深入分析丙纶纺丝计量泵的节能技术,并结合实际案例量化节能效果,为企业选型和技改提供参考。
二、计量泵能耗构成与节能潜力
1. 能耗主要来源
能耗类型 占比 影响因素
---
机械摩擦损失 40%-50% 齿轮啮合精度、轴承润滑状态
熔体内泄漏损失 30%-40% 齿轮间隙、泵体密封性
驱动系统损耗 10%-20% 电机效率、传动方式
2. 节能潜力分析
通过技术改进,可实现以下节能目标:
- 降低摩擦损失→节能10%-15%
- 减少内泄漏→节能8%-12%
- 优化驱动系统→节能5%-10%
三、高效节能计量泵的关键技术
1. 结构优化设计
(1)高精度齿轮啮合技术
- 采用渐开线修形齿轮(ISO 2级精度),减少啮合摩擦。
- 齿面抛光处理(Ra≤0.2μm),降低熔体粘滞阻力。
- 案例:某企业改用高精度齿轮后,泵效率提升12%,电耗下降9%。
(2)流道优化设计
- 螺旋式进料口:减少熔体流动阻力(压力损失降低15%)。
- 对称式出料腔:避免局部涡流,能耗降低7%。
2. 新型材料应用
部件 节能材料 节能效果
齿轮 碳化硅涂层齿轮 摩擦系数降低40%,寿命延长3倍
轴承 陶瓷混合轴承 温升减少20℃,能耗降8%
密封 石墨烯增强密封环 泄漏量<0.1%,减少补压能耗
3. 智能控制系统
(1)伺服电机直驱技术
- 相比传统变频电机,伺服系统:
- 响应速度提升50%
- 转速控制精度±0.05%
- 综合节能15%-20%
(2)压力-流量闭环控制
- 通过PID算法实时调节转速,避免过量输送(节能5%-10%)。
四、节能效果量化分析
1. 理论计算模型
泵的轴功率(P)计算公式:
P = frac{Q times Delta P}{600 times eta} quad (text{单位:kW})
其中:
- ( Q ) = 流量(cm³/min)
- ( Delta P ) = 压差(MPa)
- ( eta ) = 总效率(含机械、容积效率)
案例对比:
参数 传统泵 节能泵 差异
流量Q 2000 2000 相同
压差ΔP 30 28 -6.7%
总效率η 75% 85% +13.3%
轴功率P 133.3kW 109.8kW -17.6%
2. 实际生产数据
某年产2万吨丙纶FDY企业技改前后对比:
指标 改造前 改造后 节能效果
单泵功耗 142kW 115kW 19%↓
吨丝电耗 380kWh 308kWh 72kWh↓
年节电收益 - 144万度 约86万元
五、系统级节能策略
1. 多泵协同控制
- 主从泵联调:根据生产线负载动态启停备用泵,避免低效运行。
- 案例:某企业通过智能联控,系统能耗再降8%。
2. 余热回收利用
- 将泵体高温(200-250℃)余热用于预热熔体,降低加热能耗10%-15%。
3. 预防性维护
- 定期监测齿轮磨损(振动分析)、密封状态(压力衰减测试),避免能效下降。
六、行业前沿技术展望
1. 磁悬浮驱动计量泵
- 无机械接触,摩擦损失趋近于0(实验室阶段节能40%+)。
2. 数字孪生优化
- 通过虚拟仿真提前预测能耗瓶颈,优化泵的运行参数。
3. 纳米流体润滑技术
- 在熔体中添加纳米颗粒(如SiO₂),降低流动阻力15%-20%。
七、结论与建议
1. 节能效益总结
通过综合应用高效泵技术,丙纶纺丝企业可实现:
- 单泵节能15%-25%
- 吨丝生产成本降低50-100元
- 投资回收期<2年
2. 选型与技改建议
- 优先选择:伺服直驱+高精度齿轮+陶瓷轴承组合。
- 改造重点:传统泵可优先升级密封和驱动系统。
- 长期规划:逐步引入智能监控和余热回收系统。
随着材料科学和智能控制技术的发展,计量泵的节能潜力还将进一步释放。企业应建立全生命周期的能效管理体系,持续挖掘降耗空间。