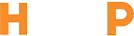

一、丙纶输送泵概述
丙纶输送泵是一种专门用于输送聚丙烯纤维(丙纶)及其相关溶液的专用设备,广泛应用于化纤、纺织、石油化工等行业。作为现代工业生产中的重要输送设备,丙纶输送泵凭借其优异的耐腐蚀性能、稳定的输送能力和高效的作业效率,已成为丙纶生产流程中不可或缺的关键设备。
丙纶(聚丙烯纤维)作为一种重要的合成纤维材料,具有比重轻、强度高、耐化学腐蚀性好、电绝缘性能优良等特点,广泛应用于绳索、渔网、地毯、非织造布等领域。在丙纶的生产过程中,从原料准备到纺丝成型,需要经过多个工艺环节,而丙纶输送泵则承担着将原料、熔体或溶液在不同工序间稳定输送的重要任务。
与传统输送泵相比,丙纶输送泵在材料选择、结构设计和性能参数等方面都有特殊要求。由于丙纶溶液或熔体通常具有较高的粘度和一定的腐蚀性,这就要求输送泵必须具备良好的耐温性、耐腐蚀性和耐磨性。同时,为了确保最终产品质量,泵的输送过程必须稳定、均匀,不能出现脉冲或断流现象。
随着丙纶生产工艺的不断进步和产能的持续扩大,对丙纶输送泵的性能要求也越来越高。现代丙纶输送泵正朝着高效节能、智能控制、长寿命免维护等方向发展,以满足日益严苛的工业生产需求。
二、丙纶输送泵的工作原理
1. 基本工作机理
丙纶输送泵的核心工作原理基于容积式泵的输送机制,通过周期性改变泵腔容积来实现液体的吸入和排出。具体工作过程可分为四个阶段:
容积扩张与吸入阶段:当泵的传动机构带动内部运动部件(如螺杆、齿轮或活塞)移动时,泵腔的密闭容积逐渐扩大,形成局部低压区。在压差作用下,丙纶溶液或熔体从进口管道被吸入泵腔内部。
密闭输送阶段:吸入完成后,运动部件的继续运转将使吸入的介质被封闭在两个运动部件之间或运动部件与泵壳之间的密闭空间内。此时介质随着运动部件的移动而向出口方向转移,但尚未开始排出。
容积压缩与排出阶段:随着运动部件的进一步移动,密闭空间的容积开始减小,对内部介质产生挤压作用,当压力超过出口管道阻力时,介质被强制输送到出口管路中。
过渡阶段:在完成一次排出后,运动部件继续运转回到起始位置,准备下一个工作循环。这一过程中,设计精良的丙纶输送泵会确保各阶段平稳过渡,避免压力波动和流量脉动。
2. 不同类型丙纶输送泵的工作原理差异
螺杆泵:作为丙纶输送中最常用的泵型,螺杆泵依靠精确啮合的螺杆转子在泵壳内的旋转运动来输送介质。单螺杆泵由橡胶定子和金属转子组成,转子在定子内作行星运动,形成连续密闭腔室;双螺杆和三螺杆泵则通过精密配合的螺杆相互啮合,推动介质轴向移动。螺杆泵特别适合高粘度丙纶熔体的稳定输送。
齿轮泵:齿轮泵利用两个相互啮合的齿轮在泵壳内的旋转运动来输送液体。在吸入侧,齿轮脱离啮合时容积增大形成真空吸入介质;在排出侧,齿轮重新啮合使容积减小而压出介质。齿轮泵结构紧凑,适合中等粘度丙纶溶液的输送,但对介质清洁度要求较高。
柱塞泵:柱塞泵通过柱塞在缸体内的往复运动改变工作容积,配合进出口阀门的启闭实现介质输送。柱塞泵能够提供很高的排出压力,适合需要高压输送的丙纶生产环节,但流量波动较大,通常需要配备稳压装置。
3. 丙纶特性的特殊考量
丙纶溶液或熔体具有一些独特的物理化学性质,这对输送泵的工作性能提出了特殊要求:
高粘度特性:丙纶熔体在加工温度下的粘度通常很高,这导致流动阻力大,需要泵具有较强的剪切输送能力和足够的驱动功率。同时,高粘度流体在泵腔内容易产生较大的内摩擦热,需要考虑额外的冷却措施。
温度敏感性:丙纶在高温下容易发生热降解,因此输送过程中必须精确控制温度。泵的设计需要考虑保温或加热装置,确保介质温度稳定在工艺要求的范围内,通常控制在200-300℃之间。
剪切敏感性:过大的剪切力会导致丙纶分子链断裂,影响最终产品性能。因此,丙纶输送泵应设计为低剪切类型,螺杆泵因其温和的输送特性而成为首选。
腐蚀性考虑:虽然纯丙纶腐蚀性不强,但某些添加剂或工艺条件可能使介质具有一定的腐蚀性。泵的过流部件通常需要采用不锈钢或特殊合金材料,极端情况下甚至需要使用哈氏合金或钛材。
三、丙纶输送泵的结构组成
1. 主要结构部件
泵体:作为泵的主要支撑结构,泵体通常由高强度铸铁、不锈钢或特殊合金铸造而成,具有良好的刚性和耐压能力。泵体内部加工有精确的腔室,与运动部件形成密闭工作空间。为适应高温工作环境,泵体往往设计有保温夹套或加热装置。
转子系统:这是丙纶输送泵的核心工作部件。在螺杆泵中,转子系统由单根或多根精密螺杆组成;在齿轮泵中,则为相互啮合的齿轮副。转子材料需具备高强度、耐磨性和一定的耐腐蚀性,常用氮化钢、工具钢或不锈钢制造,表面经过硬化处理以提高寿命。
轴承系统:负责支撑转子并承受轴向和径向载荷。由于工作环境温度高且可能接触介质,丙纶输送泵的轴承系统通常采用特殊设计,如带冷却腔的双列滚子轴承或静压轴承,并配备高性能润滑系统。
密封装置:防止介质泄漏的关键部件。根据工作压力和温度不同,可能采用机械密封、填料密封或特殊密封形式。高温高压工况下,常采用双端面机械密封并配备阻封液系统,确保完全无泄漏。
驱动装置:包括电机、减速器和联轴器等,为泵提供动力。丙纶输送泵通常需要配备变频电机,以便根据工艺需求精确调节流量。大功率泵还可能配备液压马达或蒸汽轮机作为驱动源。
2. 辅助系统
加热/冷却系统:维持介质温度稳定的关键。泵体通常设计有夹套,可通入导热油或蒸汽加热,或通水冷却。温度传感器和控制系统确保介质温度保持在设定范围内,波动不超过±1℃。
润滑系统:对于大型高压丙纶输送泵,独立的强制润滑系统必不可少。它包括油泵、过滤器、冷却器和压力调节装置等,确保轴承和传动部件在高温下获得充分润滑。
清洗系统:用于停机后的泵体清洗,防止残留介质固化堵塞流道。通常包括溶剂储罐、循环泵和喷嘴等,可进行CIP(在位清洗)操作。
监测控制系统:现代丙纶输送泵配备多种传感器,实时监测压力、温度、流量、振动等参数,并通过PLC或DCS系统实现自动控制和故障诊断。
3. 特殊结构设计
流道优化设计:丙纶输送泵的内部流道经过CFD(计算流体力学)优化,避免死角或湍流区,确保介质平稳流动,减少降解风险。进口通常设计为喇叭形,减小吸入阻力;出口则可能配备整流装置,消除流动脉动。
耐磨设计:针对丙纶熔体中的填充物或添加剂可能造成的磨损问题,关键部位采用耐磨衬里或表面硬化处理。如螺杆表面可能喷涂碳化钨涂层,泵体内衬耐磨合金等。
膨胀补偿设计:考虑到工作温度变化引起的热膨胀,泵体结构设计有热膨胀补偿机构,如挠性支撑或膨胀节,防止热应力导致变形或泄漏。
模块化设计:现代丙纶输送泵趋向模块化设计,便于快速更换易损部件。如将机械密封设计为 cartridge形式,可在不拆卸泵体的情况下更换密封组件。
四、丙纶输送泵的工作特性
1. 流量-压力特性
丙纶输送泵的流量特性曲线相对平坦,即在压力变化时流量保持相对稳定,这是容积式泵的典型特征。具体表现为:
理论流量:仅与泵的几何参数(如螺杆导程、齿轮模数等)和转速有关,与出口压力基本无关。理论流量Qt可表示为:Qt = k·n,其中k为泵的排量系数,n为转速。
实际流量:由于存在内部泄漏(滑移量),实际流量Qa会随压力升高而略有下降。对于丙纶这类高粘度介质,粘度对泄漏量的影响更为显著。实际流量可表示为:Qa = Qt - C·(ΔP/μ),其中C为泄漏系数,ΔP为压差,μ为介质粘度。
容积效率:定义为实际流量与理论流量之比,是衡量泵性能的重要指标。优质丙纶输送泵在额定工况下的容积效率可达85%-95%。容积效率随粘度增加而提高,随压力升高而降低。
2. 功率特性
轴功率:泵的轴功率P由流体功率Pf和机械损失功率Pm组成。流体功率与流量和压差成正比:Pf = Q·ΔP。机械损失主要来自轴承摩擦、轴封摩擦和转子与介质的剪切摩擦。
粘度影响:介质粘度增加会导致两方面影响:一方面减少了内部泄漏,提高了容积效率;另一方面增大了剪切阻力,增加了机械损失。对于丙纶输送泵,存在一个最佳粘度范围(通常为500-5000cP),此时总效率最高。
温度影响:温度升高会降低介质粘度,从而影响泵的性能。丙纶熔体温度每升高10℃,粘度可能下降15%-20%,这会导致泄漏量增加,容积效率降低。因此,精确控制温度对保持泵的稳定性能至关重要。
3. 特殊工作特性
剪切稀化效应:丙纶熔体属于非牛顿流体,具有剪切稀化特性,即在强剪切作用下表现粘度降低。这一特性使得泵在实际工作中,转子高速旋转区域的介质粘度低于平均粘度,有利于降低驱动功率。
压力脉动:虽然容积式泵理论上能提供稳定流量,但实际工作中仍存在微小压力脉动。丙纶输送泵通常将压力脉动控制在±2%以内,以免影响下游纺丝质量。多螺杆泵和带稳压器的柱塞泵在这方面表现更优。
最小工作压力:为避免高粘度丙纶熔体在泵腔内产生过大剪切热,通常需要维持一定的出口背压(通常不低于0.3MPa)。这可通过在出口管路设置背压阀来实现。
启动特性:冷态启动时介质粘度极高,需要降低启动转速或预先加热泵体。现代丙纶输送泵通常配备慢转启动功能,待介质温度达到工艺要求后再逐步提高至工作转速。
五、丙纶输送泵的应用领域
1. 丙纶生产过程中的应用
原料输送环节:在丙纶生产的初始阶段,输送泵用于将液态丙烯或催化剂等原料精确输送到聚合反应器中。这一环节对泵的计量精度和密封性能要求极高,通常采用特殊设计的计量泵或屏蔽泵。
聚合物流送:聚合反应生成的聚丙烯熔体需要输送到后续处理工序。由于熔体温度高(200-280℃)、粘度大,通常采用高温螺杆泵,配备强力加热系统和高压密封装置。
纺丝计量输送:这是丙纶纤维成型的关键环节,熔体泵将聚丙烯熔体精确计量并输送到纺丝箱体。此处的计量泵要求流量稳定性极高(波动小于±0.5%),并能承受15-30MPa的工作压力。齿轮计量泵和高压螺杆泵是常见选择。
溶剂回收系统:在溶液法丙纶生产中,输送泵用于溶剂的回收和循环利用。这类泵需要具备良好的耐化学腐蚀性和气液两相输送能力,通常选用特殊结构的离心泵或旋涡泵。
2. 不同工艺中的泵选型
熔融纺丝工艺:这是丙纶生产的主流工艺,采用高温螺杆泵作为主输送设备。对于细旦丝生产,需要配备高精度计量泵;对于BCF(膨体连续长丝)生产,则需要大流量高压泵。
溶液纺丝工艺:主要用于生产超细旦丙纶纤维,采用耐溶剂腐蚀的磁力驱动泵或屏蔽泵,避免溶剂挥发和环境污染。
熔喷非织造布生产:需要将聚丙烯熔体超细纤维化,采用特殊设计的高压熔体泵,工作压力可达50MPa以上,通常为多级柱塞泵或超高压力齿轮泵。
复合纺丝系统:生产皮芯型或并列型复合纤维时,需要多台精密计量泵同步工作,各泵之间的流量比控制精度要求极高(误差小于0.1%)。
3. 特殊应用场景
高填充丙纶输送:当丙纶中含有高比例碳酸钙、滑石粉等填充物时,介质磨损性极强,需要选用耐磨型输送泵,如内衬陶瓷的螺杆泵或特殊硬化处理的齿轮泵。
导电丙纶生产:添加碳黑或其他导电填料的丙纶熔体具有特殊流变性能,需要低剪切输送泵以避免填料分布不均,通常选择大导程单螺杆泵。
阻燃丙纶加工:含阻燃剂的丙纶熔体可能具有腐蚀性,泵的过流部件需要采用不锈钢或镍基合金,密封系统也需特殊设计以防止腐蚀性气体泄漏。
再生丙纶处理:回收料加工的丙纶熔体通常含有杂质,需要在泵前安装高精度过滤器,并选用抗堵塞能力强的泵型,如大通道单螺杆泵或往复式柱塞泵。
六、丙纶输送泵的选型要点
1. 介质特性考量
粘度范围:这是选型的首要参数。低粘度(<1000cP)丙纶溶液可选齿轮泵或离心泵;中粘度(1000-10000cP)适合通用螺杆泵;高粘度(>10000cP)熔体则需要特殊设计的大扭矩螺杆泵。值得注意的是,丙纶熔体的粘度随温度变化显著,选型时应考虑工作温度下的实际粘度。
温度要求:根据工艺温度选择泵的耐温等级。常温输送选用普通密封;80-150℃需加热型泵体;150-250℃需要高温密封系统;>250℃则需特殊冷却设计。同时要考虑热膨胀对泵运行的影响。
腐蚀性质:分析介质中的腐蚀成分,如添加剂、催化剂残留等。普通丙纶可选碳钢泵体;含卤素阻燃剂需不锈钢;含酸性成分可能需要哈氏合金。密封材料也要相应选择,如PTFE、全氟橡胶等。
固体含量:对于填充丙纶或再生料,需考虑固体颗粒的大小、硬度和含量。少量细小颗粒(<5%,<50μm)可选用常规泵;高含量或大颗粒则需要特殊设计的耐磨泵,如硬化转子或可调节间隙结构。
2. 工艺参数匹配
流量需求:根据生产线产能确定泵的流量范围,并考虑20%左右的余量。对于流量波动大的场合,建议选用变频调速泵。计量应用则需要选择精度等级高的泵型(如±0.5%)。
压力要求:系统总压力包括管道阻力、过滤器压降、设备背压等。一般纺丝系统需要1-5MPa;熔喷非织造布可能需要10-50MPa。选型时泵的额定压力应为最大工作压力的1.2-1.5倍。
剪切敏感性:对分子链易受损的高端丙纶产品,应选择低剪切泵型,如大导程单螺杆泵。评估指标包括剪切率、平均停留时间和最大剪切应力等。
脉冲要求:纺丝等精密工艺要求流量稳定,压力脉动应控制在±1%以内。可选用多螺杆泵、带脉动阻尼器的柱塞泵或双泵并联交错运行方案。
3. 结构配置选择
密封形式:根据介质价值和毒性选择。无毒低温可选用填料密封;高温高压选择机械密封;剧毒或昂贵介质选择双机械密封或磁力耦合无密封泵。考虑设置泄漏检测和收集系统。
材料组合:转子-定子材料配对要考虑耐磨性和兼容性。常见组合如:氮化钢螺杆配不锈钢泵体;工具钢齿轮配青铜侧板;特殊场合可使用碳化硅对碳化硅的摩擦副。
驱动方式:小功率(≤30kW)可直接驱动;中功率(30-100kW)建议配减速机;大功率(>100kW)可能需要液压驱动。防爆区域需选用防爆电机。
辅助功能:根据工艺需要选择加热/冷却形式(电加热、导热油、蒸汽夹套);考虑是否集成过滤器、安全阀、压力传感器等附件;自动化程度要求(本地控制、远程监控、智能调节)。
4. 经济性评估
初始成本:包括泵本体价格、驱动系统、辅助设备和安装费用。高端材料(如哈氏合金)可能使成本增加3-5倍,但可大幅延长使用寿命。
运行成本:评估能耗(不同泵型效率差异可达20-30%)、维护频率、易损件寿命等。高效率泵虽然初始投资高,但长期运行可节省大量能源费用。
维护成本:考虑备件获取难度、更换复杂度和停机损失。模块化设计的泵虽然价格较高,但可大幅减少维护时间和成本。
生命周期:评估在预期工况下的预期使用寿命。优质丙纶输送泵在正常维护下可运行8-10年,而低质泵可能2-3年就需要大修或更换。
七、丙纶输送泵的操作与维护
1. 正确操作规范
启动前准备:检查联轴器对中和防护罩安装情况;确认润滑系统油位和油质达标;验证旋转方向是否正确;对于高温泵,应提前预热泵体至工作温度(升温速率通常控制在50℃/h以内);检查冷却系统是否畅通;确保进口过滤器清洁无堵塞。
启动程序:全开进口阀门,微开出口阀门;点动试车确认无异常;低速启动后逐渐提速至工作转速;缓慢调节出口阀门至所需工作压力(避免突然升压);监测电流、压力、温度等参数是否正常;检查密封处泄漏量是否在允许范围内。
正常运行监控:定期记录进出口压力、温度、流量和电流值;监听泵运转声音是否异常;检查轴承温度(通常不超过75℃);监测振动值(一般要求≤4.5mm/s);观察密封泄漏情况;注意润滑系统工作状态。
停机程序:逐步降低转速至最小值;关闭出口阀门;切断电源;高温泵应保持冷却系统运行至泵体温度降至安全范围(通常<80℃);长时间停机需排空泵内介质并进行清洗;寒冷环境需排净冷却水防冻。
2. 日常维护要点
润滑管理:按说明书要求周期更换润滑油(通常首次运行200小时更换,以后每2000-4000小时更换);定期检查油位和油质;高温泵应选用合成耐高温润滑脂;注意观察轴承润滑情况,防止缺油或油脂老化。
密封维护:机械密封应定期检查端面磨损情况;监测密封泄漏量,异常增大时应及时处理;填料密封需要定期调整压紧度,保持适度泄漏(约10-30滴/分钟);双机械密封要确保阻封液系统正常工作。
易损件更换:根据运行时间或磨损情况定期更换转子、衬套、轴承等易损件;螺杆泵定子通常每12-24个月需要更换;齿轮泵侧板间隙超过允许值(通常0.1-0.2mm)时应更换;建立关键备件库存,减少停机时间。
清洁保养:定期清洗泵内外表面,防止灰尘积聚;保持冷却水道畅通;每次处理不同颜色或牌号丙纶时应彻底清洗泵腔;长时间停机应注入保护油防锈。
3. 常见故障处理
流量不足:可能原因包括进口过滤器堵塞、进口管路泄漏、转速不足、介质粘度变化、内部磨损间隙过大等。处理措施:清洗过滤器、紧固连接、检查驱动系统、调整温度或更换高粘度介质、检修更换磨损件。
压力波动:可能由进口供料不稳定、气体混入、安全阀故障、运动部件损坏等引起。应对方法:检查前序设备、排气处理、校验安全阀、停机检查内部零件。
异常振动噪音:常见原因有轴承损坏、对中不良、汽蚀现象、部件松动或磨损、基础刚度不足等。解决步骤:检查并更换轴承、重新对中、提高进口压力或降低转速、紧固松动部件、加固基础。
密封泄漏超标:机械密封失效、填料磨损、轴套磨损、压力突增等都可能导致。处理方案:更换密封件、调整或更换填料、修复或更换轴套、检查系统压力波动原因。
过热现象:可能源于冷却不足、润滑不良、过度摩擦、介质温度过高等。应对措施:检查冷却系统、改善润滑条件、调整运动部件间隙、降低介质温度或泵转速。
4. 专业维护建议
状态监测:实施振动监测、温度监测和性能监测等预知性维护技术;建立趋势分析档案,提前发现潜在故障;关键泵可安装在线监测系统。
专业维修:复杂故障应交由厂家或专业维修团队处理;精密部件如螺杆、齿轮的维修需要专用设备和工艺;密封更换应遵循严格的操作规程。
性能测试:大修后应进行性能测试,包括流量-压力特性、效率、振动噪音等指标,确保恢复出厂标准;必要时可进行第三方检测认证。
技术升级:关注泵技术发展,适时进行节能改造或智能化升级;如将普通机械密封升级为智能密封系统,加装变频控制系统等。
八、丙纶输送泵的发展趋势
1. 高效节能技术
高效水力设计:通过CFD流体仿真优化流道和转子型线,减少湍流和涡流损失。新一代丙纶输送泵的效率可提升5-8%,如采用非对称双螺杆型线设计的泵比传统设计节能10%以上。
智能调速系统:将变频驱动与工艺参数联动,实现流量-压力的精确匹配。智能调速可避免节流损失,典型应用可节能20-30%。部分先进系统还能学习生产规律,自动优化运行参数。
低摩擦技术:应用新型轴承材料(如陶瓷轴承)、表面处理技术(如DLC类金刚石涂层)和优化润滑系统,降低机械损失。磁悬浮轴承技术的引入可完全消除机械接触摩擦,特别适合高速精密输送。
废热回收利用:开发带热回收功能的泵系统,将机械损失产生的热量用于工艺加热。如某德国品牌的熔体泵可将70%的"废热"重新利用,整体能效提升15%。
2. 智能化发展
物联网集成:新一代丙纶输送泵配备多种传感器,实时监测压力、温度、振动、泄漏等参数,通过工业物联网(IIoT)技术实现远程监控和预测性维护。如西门子的智能泵系统可提前2-3周预测轴承故障。
自适应控制:基于AI算法的智能控制系统能自动适应介质特性变化(如粘度波动)、自动优化运行参数、自动诊断常见故障。如Nordson的Adaptive Pumping技术可实时调整转速补偿粘度变化。
数字孪生技术:为每台泵创建数字孪生体,在虚拟环境中模拟各种工况,用于性能优化、故障预测和操作培训。此技术可将意外停机减少40%,维护成本降低25%。
区块链应用:建立泵的全生命周期区块链档案,记录设计、制造、运行、维护等全流程数据,实现备件溯源和质量追踪,提升供应链透明度。
3. 新材料应用
高性能合金:镍基合金(如哈氏合金)、钛合金等耐腐蚀材料在特殊丙纶工艺中的应用扩大。粉末冶金技术制造的微晶合金转子寿命可达传统材料的3倍。
工程陶瓷:碳化硅、氧化锆等陶瓷材料用于极端工况。全陶瓷机械密封可在无润滑条件下工作,寿命比传统密封长5-10倍;陶瓷衬里泵可耐受强磨损性填充丙纶。
复合材料:碳纤维增强聚合物(CFRP)用于制造轻量化转子,比金属转子轻60%且耐腐蚀;PTFE复合材料用于制造耐化学腐蚀定子,适合处理含强溶剂的丙纶溶液。
自修复材料:研发中的微胶囊自修复材料可在泵内部件出现微裂纹时自动释放修复剂,延长关键部件使用寿命。这类材料有望将泵的大修周期延长50%以上。
4. 专业化定制
模块化设计:将泵分解为标准模块,便于快速配置不同规格。如一家瑞士制造商提供"乐高式"螺杆泵,客户可自行组合不同直径的转子和长度的泵体,满足特定流量压力需求。
微型化发展:为实验室研发和小批量特种丙纶生产开发微型精密输送泵,流量范围可低至0.1ml/min,压力稳定性达±0.1%,用于高端医用丙纶纤维的研发生产。
多功能集成:将传统单一功能的泵发展为集输送、混合、反应于一体的多功能设备。如某意大利公司推出的"反应输送泵"可在输送过程中完成丙纶改性添加剂的均匀分散。
极端条件适应:开发适应超高温(>400℃)、超高压(>100MPa)或超高粘度(>1,000,000cP)等极端工况的特种泵,满足航空航天等高端领域对特种丙纶的需求。
随着丙纶应用领域的不断拓展和工艺技术的持续进步,丙纶输送泵将朝着更高效、更智能、更专业的方向发展,为化纤行业提供更优质的流体输送解决方案。未来的丙纶输送泵不仅是简单的输送设备,更将成为集成传感、控制、优化功能的智能化生产单元,在丙纶生产的数字化、网络化、智能化转型中发挥核心作用。